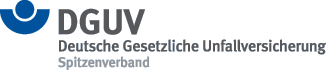
completed 10/2019
Collaborative robots allow humans and robots working together safely in a fenceless environment. According to ISO/TS 15066 and DGUV information sheet FBHM 080, safety measures must ensure that the robot cannot harm the human in any case. One way of protecting humans from serious injuries is to prevent the robot from exceeding biomechanical limit values when colliding with humans.
The German Social Accident Insurance Institution for the Woodworking and Metalworking Industries (BGHM) and Fraunhofer IFF laid the groundwork from 2015 to 2018 for defining the biomechanical limits in a variety of studies. Until 2018, it was not possible to carry out load tests on body locations on the head, neck, chest and abdomen, since the physicians involved were unable to assess the health risks for the subjects using limited data from literature. Once Fraunhofer IFF finished their studies, the amount of data was sufficient and allowed the physicians to update the risk assessment, which came to the conclusion that the risk of injury is sufficiently low for experimental load tests on the non-examined body locations. This update finally allowed Fraunhofer IFF to continue with the load tests.
The purpose of this study was to continue the tests. Its objective was to examine the body locations of ISO/TS 10566, which belong to head, neck, chest and abdomen, concerning the onset of pain under clamping and impact loads over blunt or semi-sharp surfaces, and then, to specify the missing limit values.
The study design pursued the approach to conduct load tests with volunteers. Fraunhofer IFF used an algometer and a pendulum to apply clamping and impact loads to the considered body locations. During a single load test, the test supervisor increased the load intensity applied to the volunteer slowly until they sensed a slight painful feeling at the stressed body location.
Fraunhofer IFF used two different contact bodies to apply the load. The first contact body was made of aluminum and simulated the effect of a semi-sharp surface, because of its small size and square face. The second contact body was made of a compliant foam, which distributed force evenly within the contact area and thus simulated a blunt contact. In addition to the regular group of volunteers, Fraunhofer IFF also examined a control group. The test procedure was the same used by the Johannes Gutenberg University Mainz (JGU) in a volunteer study from 2011 to 2014. The purpose of the extra tests was to demonstrate whether the results from Fraunhofer IFF and JGU were comparable.
The regular group of volunteers consisted of 10 male and 10 female volunteers. Fraunhofer IFF tested the group with clamping and impact loads on all body locations of the head, neck, chest, and abdomen. The control group consisted of 5 male and 5 female volunteers and passed only clamping tests but on all body locations of ISO/TS 15066.
Fraunhofer IFF used the third quartile of the empirical distributed results to define the desired limit values. It then combined them with the limit values from the previous studies, leading to the final list of limit values for all body locations, all load forms, and all contact types distinguished by ISO/TS 15066. The mean thresholds from the control group based on the maximum contact force equal in most cases those from the JGU study, and indicate that both sites received comparable results. The mean thresholds based on the maximum pressure from the JGU study, however, were significantly higher than those of Fraunhofer IFF.
-cross sectoral-
Type of hazard:mechanical hazards
Catchwords:man-machine interface, equipment safety, machine safety
Description, key words:Human-robot collaboration