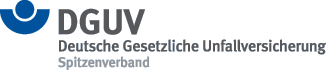
completed 06/2012
In certain applications on plant and machinery, a drawback of the familiar non-contact protective devices such as light curtains or laser scanners is their low acceptance, owing to their inadequate flexibility for adaptation to automated production processes. Since a human being is detected by this type of sensor only in two dimensions, for example in the leg region, the result is often relatively high safety distances between human and machine: in this case, the provisions of standards require an additional safety distance to allow for an arm extended in the direction of the hazard point. For these reasons, and also because vision systems are regarded as low-cost sensors for the safeguarding of larger hazard areas, industry is stepping up its efforts to develop such systems. Knowledge of the safety requirements placed upon such systems and practical experience gained with them is currently limited or non-existent. The general suitability of vision systems for safety applications for the safeguarding of machines and installations, such as robots, is considered within the project. Initial insights are to be gained with 3D cameras concerning their potential for use in the future as protective devices.
Systematic studies into the integrity of detection by vision systems are planned on at least one industrial product. The focus lies upon the consideration of environmental influences, such as extraneous light; at the same time, attention is to be paid to adequate in-plant availability. A newly developed 3D camera system which employs time of flight measurement on each individual pixel is to be examined in greater detail. Possible issues in this context are the creation of a software tool for systematic analysis of distance measurement data, a study of the measurement accuracy (e.g. under the influence of temperature), the reflectivity of objects, and a software interface for demonstration of the 3D camera's function as a safety device.
The reliability of detection on a camera system with test pattern detection intended for use as protective equipment was studied, yielding a positive result. The product was certified in the course of a further test. The review of a concept for a stereo camera system was also passed. The results of the studies have been submitted to international standardization activity. The existence of two tested systems (a second system was tested by the test body of the Institution for Social Accident Insurance in the metal- and woodworking industry) has revived interest in standardization at international level of protective devices of this kind. The greatest interest has been expressed by the German representatives. Preliminary drafts of a revised version of IEC 61496-4 (Part 4: Particular requirements for equipment using vision based protective devices (VBPD)) have already been formulated. With regard to their scope, these drafts refer precisely to the two systems studied at the IFA. PMD (photonic mixing device) cameras deliver a measured distance value for each individual pixel of the camera, thereby yielding a three-dimensional image of the environment. Intended markets for these devices lie in the areas of automation, autonomous vehicles, human-machine interaction and quality control. Whether this list may also be extended to include safety technology in the area of machinery and plant equipment is not yet clear. As yet, the measurement principle of distance information gained by phase comparison measurement has not been proved suitable for safety-related applications. The various industrial partners consulted have not as yet been able to present a concept that is robust in economic and safety terms. Patent-related obstacles also exist in this area. In the future, camera systems will constitute an important addition to existing protective equipment, provided their satisfaction of the criteria for their suitability for use as safety camera systems is assured and demonstrated. A complex, safe camera system is capable of much more than conventional sensor technology: a single system assumes the functions of protection and intelligent control. In order to serve the growing market for collaborative robots, protective equipment is needed with very short response times and low resolution. The experience gained in the project shows that such products are still at the limits of what is technically feasible and economically viable.
-cross sectoral-
Type of hazard:mechanical hazards
Catchwords:accident prevention, machine safety, new technologies
Description, key words:vision system, protective device, safety, detection zone, automation, robot, 3D camera, passive pattern, standardization, IEC 61496-4