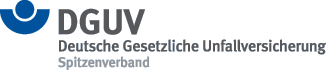
completed 03/2009
In the meat-processing industry, employees are subject to high noise exposure at many workplaces, for example in abattoirs and on sausage machines, clippers and peelers. Noise exposure presenting a hazard to the hearing may arise even in plants employing the latest, state-of-the-art machinery. Since the working areas generally have highly reflective walls, ceilings and floors, the objective here was for substantial noise reductions to be achieved by means of room-acoustic measures, such as the application of sound-absorbent surfacings to ceilings and possibly also to walls. For hygienic reasons, however, open-pore sound-absorbent materials manufactured from artificial mineral fibres or foam cannot be used. All materials must be suitable for cleaning with foam-forming suds and for spraying with high-pressure cleaners. Besides considering the acoustic aspects, the project also had to examine the materials' hygienic suitability. This task was performed by the BG responsible for the meat-processing industry, with the support of the unit responsible for biological agents at the BGIA - Institute of Occupational Safety and Health.
In order for the effectiveness of sound-absorbent materials to be studied in practice, a typical, smaller meat-processing plant was selected. The existing noise impact situation was first recorded and analysed, the results being the starting-point for design of the room-acoustic measures. The first measure to be recommended was complete surfacing of the ceiling with microperforated ceiling tiles. The absorption capacity of the material was tested in the reverberation room of the BGIA. Prognostic calculations yielded substantial reductions in the sound level of 3 dB(A) and higher for the premises of the business. Since, as was shown by studies conducted by the BG responsible for the meat-processing industry, the rear of the microperforated tiles never fully dried out and hygienic problems could therefore be anticipated, an alternative material had to be found. Following a corresponding search, a foam material with a thickness of approximately 60 mm and with a thin film covering was selected. This material was bonded directly onto the ceiling surface. The improvement in the room acoustics attained by this measure and the resulting successes in noise abatement were verified both by prognostic calculations and by in-plant measurements.
Owing to the high reflectivity of the tiled and concrete floor, wall and ceiling surfaces, the room-acoustic situation in meat-processing plants is generally extremely unfavourable. In the selected model business, a reverberation time of approximately 2.3 seconds at mean frequencies was measured. This value corresponds to a very low sound absorption (average sound-absorption coefficient: approximately 0.06). The installation of a sound-absorbent ceiling consisting of foam material enabled the reverberation time to be reduced by a factor of approximately three (average sound-absorption coefficient: approximately 0.2). The result is a substantial reduction in the reverberation which is also subjectively evident. The average reduction in the level per doubling of the distance improved from the original value of 1.1 to 1.4 dB to values of 2.5 to 2.9 dB (at mean frequencies of 500 Hz to 2000 Hz). The success of the room-acoustic measure can be seen from the measurable reduction in the noise level of approximately 3 dB(A) at the workplace directly at the sausage machine. Corresponding calculations of the level distribution for the room with and without the noise-absorbent ceiling yielded noise reductions of over 4 dB(A) for the workplace at the sausage machine, and of 6 to 7 dB(A) for workplaces at greater distances from the sausage machine. During the search for suitable materials, other materials, based for example upon mineral fibres, were identified in addition to the foam material studied here. These should also satisfy the particular hygiene requirements.
food industry
Type of hazard:noise/vibrations, biological agents, questions beyond hazard-related issues
Catchwords:noise, workplace design, demography
Description, key words:noise abatement, room acoustics, absorber elements, absorption material, meat processing, hygiene