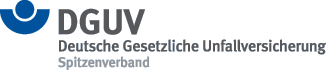
completed 08/2007
The ISO 13849-1 standard (EN 954-1: Safety of machinery - Safety-related parts of control systems - Part 1: General principles for design) is a generic machinery standard governing the structure and probability of failure of safety-related control systems. The current version, issued in 1997, defines five typical control-system architectures or "categories" (single or two-channel, tested/untested) for this purpose, independently of the technology employed (mechanical, pneumatic, hydraulic, electrical). In order for the standard to be brought into line with the assessment principles of the basic safety standard EN 61508: "Functional safety of electrical/electronic/programmable electronic safety-related systems" for electrical, electronic and programmable electronic controls, a revision of EN ISO 13849-1 was to give greater consideration to analysis of the probability of failure. The project is to assist users of the ISO 13849-1 machinery standard, by developing precisely defined and practicable methods by means of which the probability of failure of typical control-system implementations can be predicted quickly and easily. To this end, the existing concept of categories was to be embedded in a wider system. In the process, consideration had to be given to the particular aspects of the different technologies, e.g. programmable components or components subject to heavy wear.
Based upon typical control structures for the five familiar categories in EN 954-1, scientific methods (e. g. Markov modelling) were used to determine the simplest possible correlations between a control system's probability of failure and its structure, the mean time to dangerous failure of the components, the diagnostic coverage, and the resistance to common-cause failures. In order to determine these four parameters, a simple method was developed for all control technologies (mechanical, pneumatic, hydraulic and electrical) with the aid of tables, example values, simple conversion formulae and worst-case estimations. Stepped measures for software safety were integrated. Aids for manufacturers of machinery were developed, such as a PC-based tool for application of the method and example analyses of control systems.
The existing methods were made more complete within the project. A simple method was for example developed for components subject to wear (pneumatic and electromechanical components) by which number of oprerations (B10d) may be converted into the reliability values (MTTFd) used in the standard. This was supplemented by basic work on the calculation of the B10d value by analyses of the mean time to failure or by tabularized guideline values (good engineering practice). The methods were formulated for mechanical, electromechanical and fluid engineering components. Existing approaches to stepped software requirements were developed further, for example by the development of a guideline for the treatment of complete standard components employing integrated software. Experience gained with application on real-case examples of control systems resulted in the methods proposed in the standard being amended. An interpolation method was for example derived for calculation of the probability of failure. The influence of the frequency of automatic tests was also analyzed mathematically and estimated by means of a formula which can be applied easily. As an aid particularly for small and medium-sized enterprises, instructions were formulated for the transition from the existing to the future requirements of the standard. The results of the project have served in approximately equal measure for correction and supplementing of the standard on the one hand and for the production of guides to its application in practice on the other. Check lists were also developed for the testing activity. Whilst the project was still in progress, interim results were made available in the form of presentations and publications for consultations with the German Verband Deutscher Maschinen- und Anlagenbau (VDMA) and Zentralverband Elektrotechnik- und Elektronikindustrie (ZVEI) and with manufacturers and expert committees.
-cross sectoral-
Type of hazard:mechanical hazards
Catchwords:safety technology (engineering), machine safety, standardisation
Description, key words:safety of machinery, control systems, category, performance level (PL), ISO 13849-1, EN 954-1, revision, quantification, probability of failure, safety-related reliability, mean time to dangerous failure (MTTFd), diagnostic coverage (DC), common-cause failure (CCF), software, risk graph, designated architecture, safety-related parts of controls, pneumatics, hydraulics, electrics, electronics, programmable electronics, software